Ajrak Block Printing
Ajrak prints may be a distinguished sort of block printing on fabric, made of carved Wooden Printing Blocks that originated within the present-day province of Sindh, Pakistan, and neighboring Indian districts of Kutch in Gujarat and Barmer in Rajasthan. Ajrak block printing design is embedded into the culture of the people living here due to the traditions of the traditional Indus Valley Civilisation.
The process of Ajrak printing begins with designs expertly hand-carved into Wooden Printing blocks before being dipped in dye and printed on fabrics primarily of cotton and silk. The term ‘Ajrak’ is derived from the Arabic word ‘Ajrak’ which may mean ‘indigo’ or ‘blue’. This reflects Sindh’s historic reputation as a dominant producer of indigo dye and illustrates the extensive use of the indigo shade of blue in traditional Ajrak print, which is still common to this day.
Traditionally, Ajrak prints were donned by both men and ladies. To this day men continue to use Ajrak printed turbans and cummerbunds, as well as draping the fabric over their shoulders. Just as before, women still wear Ajrak print sarees, Ajrak print Kurtis printed dupattas, chadors, and shawls that exquisitely complement other garments like sarees. Men can wear Ajrak print suits.
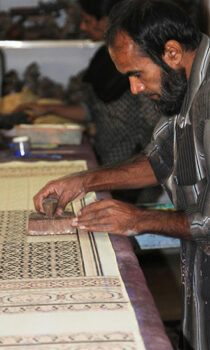
Ajrak Printing and its Timeless Motifs
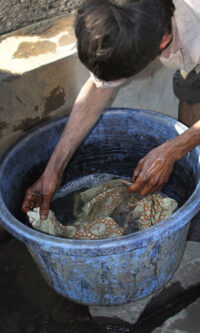
The essence of Ajrak printing is to celebrate nature in terms of the vast use of natural raw materials and resources and therefore the representation of its motifs and hues. For millennia artisans have made use of natural dyes to supply the deep intense colors of Ajrak, like extracts of the madder plant for red and extracts from the true indigo plant for the popular indigo color.
The motifs featured in Ajrak print are mainly elaborate geometric jewel-like shapes that incorporate motifs that symbolize nature, like stars and flowers. Ajrak printing may be a distinguished sort of block printing that originated within the present-day province of Sindh, Pakistan, and neighboring Indian districts of Kutch in Gujarat and Barmer in Rajasthan.
Ajrak printing is embedded into the culture of the people living here due to the traditions of the traditional Indus Valley Civilisation. The process of Ajrak fabric block printing begins with designs expertly hand-carved into wooden blocks before being dipped in dye and printed on fabrics primarily of cotton and silk. The term ‘Ajrak’ is derived from the Arabic word ‘Ajrak’ which may mean ‘indigo’ or ‘blue’. This reflects Sindh’s historic reputation as a dominant producer of indigo dye and illustrates the extensive use of the indigo shade of blue in traditional Ajrak print, which is still common to this day.
Traditionally, Ajrak prints were donned by both men and ladies. To this day men continue to use Ajrak printed turbans and cummerbunds, as well as draping the fabric over their shoulders. Just as before, women still wear Ajrak printed dupattas, chadors, and shawls that exquisitely complement other garments like sarees.
Secrets to Creating the Perfect Ajrak Print
The assembly technique is, to an extent, similar. Designs are first carved into wooden blocks before being dipped in dye and printed onto fabric. Usually, wooden blocks, referred to as bunta, utilized in the primary stage of printing are carved out of shisham, more commonly referred to as Indian blackwood, and wooden blocks utilized in the later stages of printing are carved out of teakwood.
During the monsoon season, the blocks are soaked in mustard oil to stop expansion that affects the designs that were painstakingly carved by artisans. Artisans diligently prepare the material before beginning the meticulous printing. The fabric is first washed to rid it of starch and impurities.
It is then soaked in a mixture of camel dung, seed oil, and water, which not only softens the material but also acts as a bleach. The fabric is then tied together and stored for 5-10 days, counting on the weather.
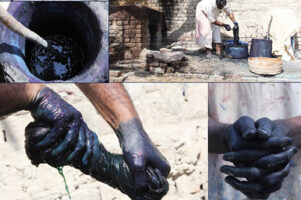
The quality of the material is often determined by the pungency of the smell that emanates from the stored fabric, which is like the favored Indian condiment, mango pickle. This is a result of the fibers of the material reacting with the seed oil.
The fabric is then laid call at the sun to dry before undergoing a second treatment of a mix containing oil and washing soda.
The fabric is then stored overnight before being washed – traditionally, this happened within the Indus – before being soaked in sakun, a mix of dried lemon, castor oil, molasses, tamarisk gall, and water. Multiple treatments make sure that the material is in a position to consistently absorb and retain dyes leading to Ajrak’s signature deep colors.
Unlike block printing, which sometimes uses wooden blocks to print dye onto fabric, the utilization of those blocks in Ajrak printing is to use a resist that outlines the planning. The fabric is laid out on a flat surface for artisans to accurately align the wooden blocks before covering the entire piece of fabric with resistance. After each application of the resist, artisans dye the material in a single color before washing and drying it for the subsequent dyeing stage employing a different color.
Artisans repeat this elaborate process until the whole piece of cloth is complete with Ajrak’s signature deep colors illuminating the intricate patterns.
If you want to read about more Indian traditional printing techniques, like the art of block printing, then click on the hyperlink.